Description
MZS05 Dimensions and Operating Range
(*1) The specifications are subject to changes without notice.
(*2) In case that an end user uses this product for military purpose or production of weapon, this product may be liable for the subject of export restriction stipulated in the Foreign Exchange and Foreign Trade Act. Please go through careful investigation and necessary formalities for export.
MZS05 General Specifications
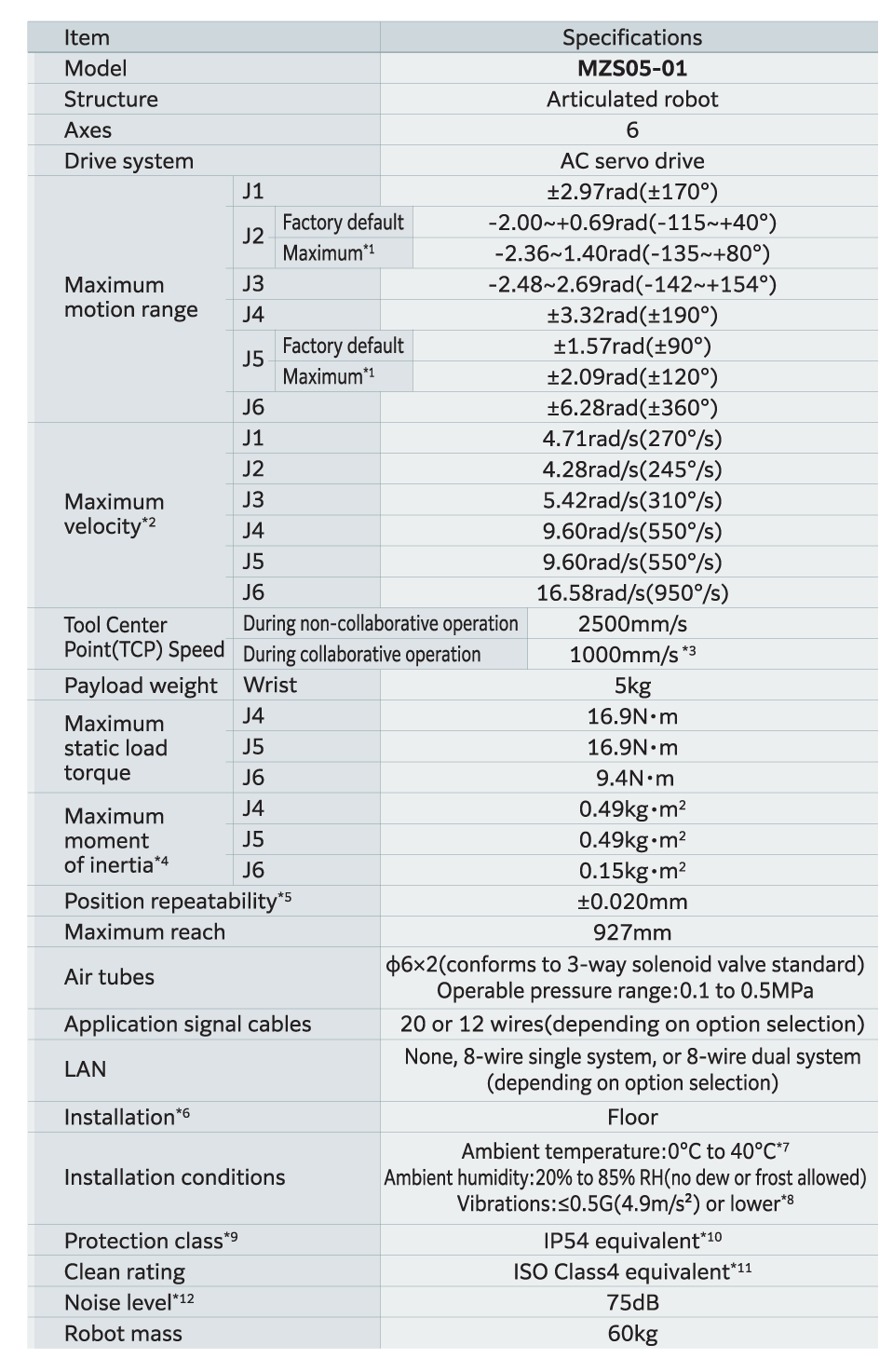
1 [rad]=180/π[°],1[N・m]=1/9.8[kgf・m]
• Note that the information represented in this document, such as rated values, specifications, and dimensions, are subject to change without notice to improve the product.
• An explosion-proof version of this product is not available.
- If the J2 and J5 axes are operated at their maximum limits, there is a risk of clamping even without tools or work. To eliminate this risk when shipped from the factory,
a robot monitoring unit (RMU50-11, complies with ISO 13849-1) is used to restrict operable range.
Modify the operable range only if you have performed a risk assessment in the actual environment in which the robot is to be used and have determined that the risk is reduced.
Depending on the loaded tools or work, there is a risk of clamping even when the operable range is restricted. - The maximum speed indicated in the table is the maximum value. Speeds are subject to change depending on factors such as the work program and wrist payload conditions.
These specifications indicate the maximum value for each item in normal recovery mode. - A risk assessment that is performed according to the basic safety standard ISO 12100 is required, and the speed at which the colliding part operates needs to be determined.
- Note that the moment of inertia varies depending on the wrist payload conditions.
- Conforms to JIS B 8432.
- The robot cannot be installed on surfaces that are at an incline of 30° or more. Ensure that the robot is installed on an incline that is less than 30°.
- In a case of usage at no higher than 1,000 m above sea level. Ambient temperature is subject to restrict at elevations that are higher than the allowable range.
- When using the robot for collaborative operation, the robot might stop due to vibrations on the floor or hand. The source of such vibrations must be eliminated before actual use.
- Liquid substances that will degrade the sticker parts on the robot cannot be used.
These include organic solvents, acids, alkaline substances, chlorinated substances, and gasoline-based cutting fluids. - Environments subject to splashing liquids or mist might trigger the proximity sensors and cause the robot to stop.
- Based on an internal assessment in accordance with ISO 14644-1.
In order to maintain the clean rating, install the robot in a clean room with downflow. Since the robot is not packaged in a dust-proof package,
it is necessary to remove dust and dust from the robot and wipe it clean when it is brought into the clean room. - This is an equivalent sound pressure level of an A weight as measured according to JIS Z 8737-1 (ISO 11201). (Operation at rated load and maximum speed)